Never forget the 3 pillars of safety
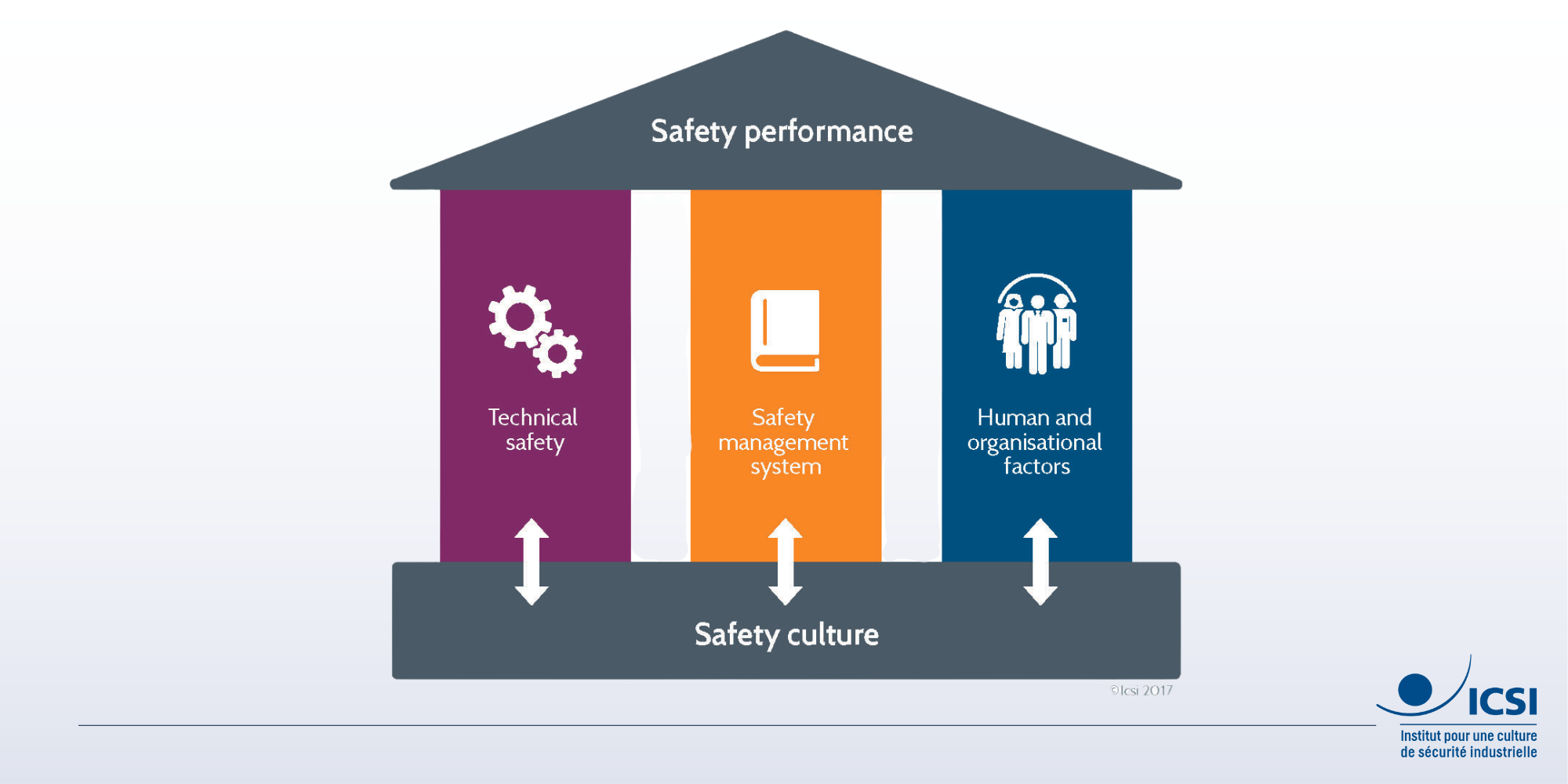
Technical reliability, safety management systems, and human and organizational factors: the 3 pillars of industrial safety. Improving an organization’s safety culture requires, amongst other things, always paying attention to these 3 pillars.
The 3 pillars of safety
Safety relies on 3 pillars:
- technical reliability,
- safety management systems,
- and human and organizational factors.
These 3 pillars have emerged as approaches to safety have evolved over time, and each dimension adds to the previous ones, to create a safety culture.
Technical reliability (1960s–1980s)
Up until around the 1960 s, the industry considered that technical reliability was the best way to reduce accident rates. They invested in reliable industrial facilities, and improvements to processes, equipment, maintenance, etc.
Prevention was primarily focused on technical barriers. Safety performance improved—and the number of accidents declined—until eventually a plateau was reached where little further progress could be made. Around this time, two major accidents (Seveso in 1976, and Three-Mile Island in 1979) led to a tightening of regulatory requirements, notably via the Seveso 1 directive in 1982.
Management systems (1980s–2000s)
In high-risk industries, the introduction of safety management systems has formalized procedures, illustrated by corporate policies, rules and procedures, indicator-based management, reporting, risk and event analysis techniques, etc. At this time, safety became the responsibility of experts. The new approach led to a second reduction in the accident rate, but this too reached a plateau. Why did this happen? Mainly because this top-down approach was driven by experts, who were too far removed from reality on the ground, and who knew little about the various other actors in the organization.
Safety management systems can sometimes have perverse effects. For example, the under-reporting of certain incidents artificially lowers the accident rate. In some industries, this leads to ‘green meadow’ syndrome: banks of indicators that always show that all is well.
Denis Besnard, Icsi expert - excerpt from the Safety Academy podcast
Human and organizational factors (from the 2000s onwards)
The introduction of human and organizational factors (HOF) marked the beginning of a new fall in the rate of industrial accidents. HOF examines the actual conditions in which human activity takes place, with respect to 4 dimensions:
• the individual;
• the workplace;
• teams;
• the organization and its management.
Even today, human and organizational factors are often an area where an organization can make progress in terms of safety. In practice, they are a lever that can be used to reduce the accident rate, by thinking about dimensions such as how the workplace is organized or the priority that is given to safety.
Never forget the 3 pillars
There are a number of points to pay attention to if we want to take effective action in the workplace. We must:
- work coherently and consistently on all 3 pillars at the same time—don’t fall into the trap of treating them in isolation;
- ensure that actions are balanced: a focus on one pillar cannot overcome insufficient action on the other two;
- manage the 3 pillars on an ongoing basis, it’s a marathon, not a sprint!