Subcontracting: the devil is often hidden in the details!
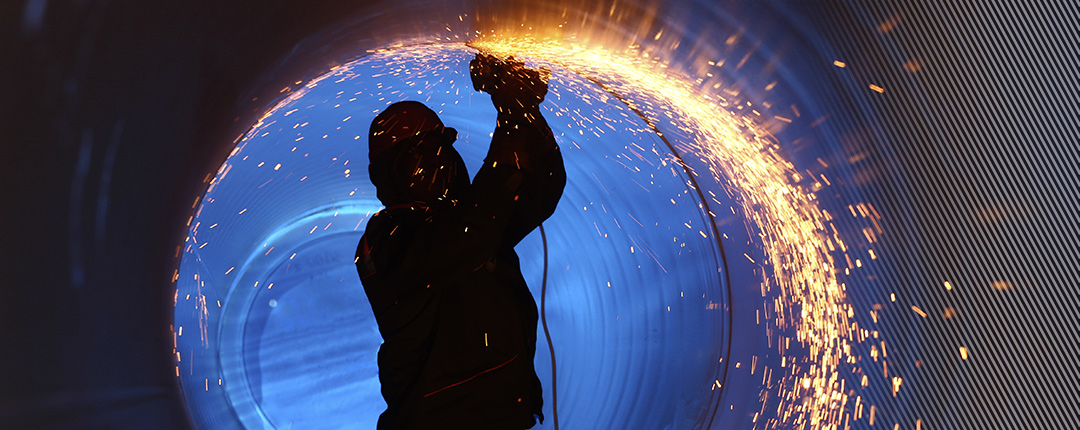
Subcontracting provides fertile ground for the exploration of safety issues. Who hasn’t already heard the classical account of the main principles of a good relationship between clients and subcontractors? But beware, the devil is often hidden in the details, as the contractual relationship develops!
The key to preventing serious, fatal and major technological accidents is that the contracting company and the subcontractor share the same vision of the most important risks.
| 4 key steps for better cooperation |
Lorem ipsum dolor sit amet et consegure not palenque. Dolor sit amet et lorem dor ipsum locas palenque et conseguret palenque. Dolor sit amet et lorem dor ipsum locas palenque et consegure. Dolor sit amet es palenque et conselor sit amet et lorem dor ipsum locas palenque et consegure.
Step 1: Upstream; choosing the service provider
Beyond what they might claim, contracting companies must look at the real safety practices of service providers who respond to a call for tenders. But how do you go about this? Well, first of all, don’t just look at the incident rate, as it doesn’t tell you much about how prepared the company is to deal with the most serious risks. Instead, you could organize a period of immersion in the field. And ensure that HSE and technical departments are given due weight in the selection process.
Step 2: During preparations; build a shared safety culture
Speaking the same language and sharing some fundamental safety practices are prerequisites for good cooperation between a contracting company and a subcontractor. Sharing views on the key rules, or at-risk operations that could have very serious consequences, or transforming a mandatory D-day visit into a genuine opportunity to talk about safety, are just some of the best practices that can be put in place.
Step 3: During execution; safety trade-offs
“Any manager who spends time in the field knows that they will discover problems that will have to be dealt with...” Not only is this true, but it’s also indispensable for prevention! It is essential to create a climate of trust that encourages feedback, especially in potentially dangerous situations. Sometimes, this feedback requires on-the-spot trade-offs, which can be a real challenge. In this context, it is important to clearly define the respective responsibilities of the contracting company and the subcontractor, and determine who is responsible for taking decisions, and at what level.
Step 4: Downstream: reviewing the project and building upon lessons learned
Feedback is a key lever for companies to continue to improve their safety practices! The contracting company, in particular, must ensure that the subcontractor feels able to share any difficulties that they encountered. These problems can be discussed and addressed, in order to be better prepared for the next project... it’s a virtuous circle!
| Going beyond conventional wisdom |
- “Subcontractors are small local or regional companies”: False! Subcontractors can be small, local companies... or multinationals! They can carry out short-term projects or be engaged on long-term contracts.
- “Contracting companies have a better safety culture”: This, widely-accepted idea is outdated! Many subcontractors have clear, mature safety practices, and can be more advanced than the companies they work for!
- “The contract is always awarded to the cheapest provider”: True – and false! Contracting companies have made great strides in the selection of providers, based on the criteria of best value for money. But there are still cases where there is a race to the bottom: when all the bids are in, the cheapest option is chosen... to the detriment of safety.

Find out more
Read ou publication "How to foster a safe, sustainable working environment with a subcontractor? Establish trust. Right from the beginning".